Exploring the World of Metal Stamping: From Design to Production
Within the realm of production, steel stamping sticks out as a specific and reliable method for shaping metal sheets into various forms with amazing consistency. From the initial style stage where intricate patterns take shape to the intricate production processes, metal marking is a mix of artistry and design. Diving right into this globe introduces an intricate interaction of creative thinking and technological proficiency, supplying a glance right into a world where advancement satisfies craftsmanship.
History of Metal Stamping
Steel stamping, a widely made use of production procedure today, has an abundant history that dates back to old times (Metal Stamping). The origins of steel marking can be traced to ancient civilizations such as the Egyptians, that made use of marking methods to embellish precious jewelry and accessories with elaborate designs. Over time, steel stamping evolved, with civilizations like the Greeks and Romans using it for creating coins and decorative things
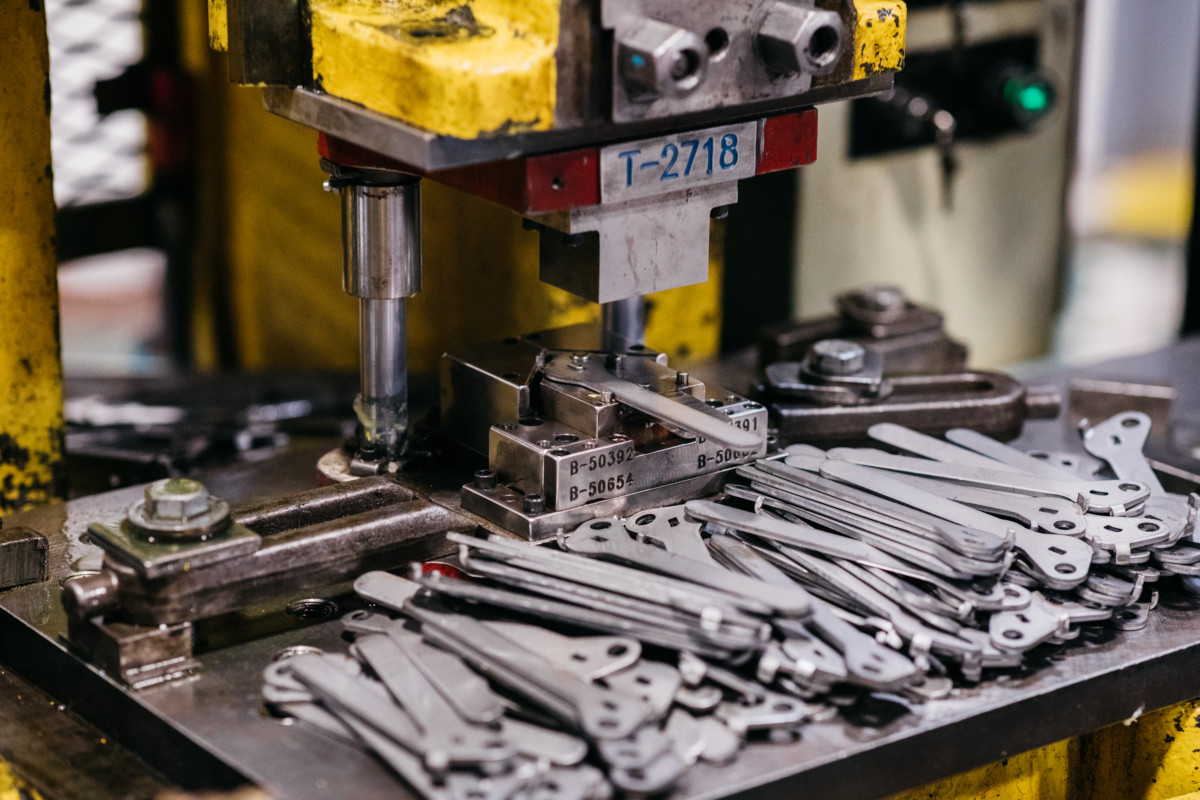
In the 20th century, metal marking continued to evolve with the assimilation of automation and computer mathematical control (CNC) technology. These improvements even more raised the effectiveness and accuracy of metal stamping procedures, making it a vital part of contemporary manufacturing throughout industries such as auto, aerospace, and electronics. Today, steel marking remains a crucial manufacturing process, incorporating tradition with advancement to meet the demands of a frequently developing sector.
Design Factors To Consider and Prototyping
Layout factors to consider in steel marking consist of product choice, component geometry, tooling style, and production expediency. Tooling style plays a considerable function in the success of metal stamping jobs, impacting part accuracy, tool longevity, and manufacturing performance.
Prototyping is a crucial phase in the steel stamping procedure that permits designers to evaluate the style, confirm manufacturability, and make necessary adjustments prior to full-scale manufacturing. By very carefully considering layout facets and using prototyping, suppliers can enhance the steel marking procedure and attain premium, cost-effective manufacturing end results.
Tooling and Devices Basics
Taking into consideration the critical function that tooling style plays in the success of metal stamping tasks, understanding the crucial devices and equipment called for is critical for attaining efficient manufacturing results. Tooling is an essential element of steel stamping, as it directly impacts the high best site quality and uniformity of the last items. Important devices include dies, strikes, and components, which are custom-made to shape and form the metal into the desired components. Passes away are the key tool made use of to reduce and create the steel, while strikes aid create openings or particular shapes. Fixtures hold the steel in position during the stamping process, ensuring precision and repeatability. Additionally, equipment such as marking presses, feeders, and coil handling systems are important for automating the stamping process and raising performance. Spending in premium tooling and tools not only boosts manufacturing performance yet also causes higher accuracy, decreased waste, and total expense savings in metal marking procedures.
Production Refine and Quality Assurance
Successfully handling the manufacturing process and implementing robust quality control procedures are essential for ensuring the success of metal stamping tasks. The manufacturing procedure in steel stamping includes a collection of actions that must be very carefully worked with to achieve optimal results.
Quality control in metal marking is paramount to supply items that satisfy the called for specifications. By preserving rigorous quality control requirements, read makers can support their online reputation for supplying top quality steel marked products.
Applications and Industry Insights
In the world of metal marking, the successful application of production processes and quality assurance steps straight affects the effectiveness and reliability of different market applications and offers useful insights right into the industry's operational dynamics. Metal marking finds widespread application across diverse sectors, consisting of automotive, aerospace, electronics, and Read Full Report devices. In the automotive industry, metal stamping plays a critical role in creating components such as framework, brackets, and structural get rid of high accuracy and performance. The aerospace sector depends on metal stamping for producing intricate parts like panels, brackets, and installations that satisfy rigid top quality standards (Metal Stamping). In the electronic devices sector, steel marking is used to produce precise elements like adapters, terminals, and heat sinks. Furthermore, steel stamping assists in the production of various household appliances, consisting of refrigerators, cleaning makers, and ovens, by giving affordable remedies for producing sturdy and intricate components. Understanding the applications and industry understandings of metal marking is essential for optimizing manufacturing procedures and boosting product high quality across different markets.
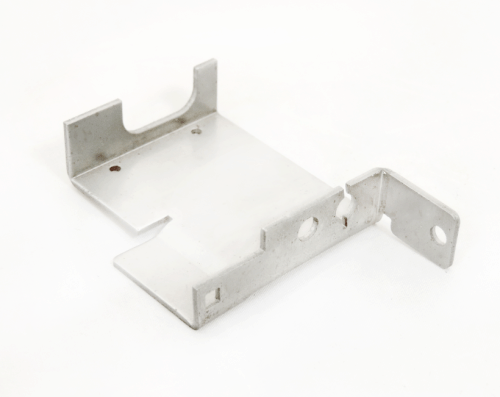
Final Thought
Style factors to consider, prototyping, tooling, equipment, manufacturing processes, and quality control are important aspects of metal marking. With its prevalent applications and market understandings, metal marking continues to be a flexible and reliable manufacturing procedure.